これから始める人、新入社員の教材になるようなものが欲しい。
どんな仕事でも初めての人は知らないところからはじまります。
ここでは鉄骨の加工業者が受注してから工場出荷までを追っていきます。
鉄骨屋(Mグレード)の流れを番号表記して一連の流れのわからない新規の人にも知ってもらえます。
- 制作工程図
- 責任者の選出
- 1・設計図書(仕様書・設計図)
- 2・製作会議(質疑事項/問題抽出)
- 3・溶接計画
- 4・検査要領
- 5・製作要領書
- 6・工作図・加工図
- 7・照合チェック
- 8・修正
- 9・承諾申請
- 10・出図
- 11・鋼材・購入品発注明細
- 12・鋼材発注
- 13溶接材料発注
- 14・購入品発注
- 15・入庫・受入検査
- 16・作業者(材料管理責任者)
- 17・溶接材料・購入品の受け入れ
- 18・裏当て加工
- 19・DF(ダイアフラム)加工
- 20・サイコロ(コラム)加工
- 21・H鋼(仕口)加工
- 22・スカラップ加工
- 23・シャフト加工
- 24・加工
- 25・作業者
- 26・補修
- 27・組立て
- 28・作業者
- 29・補修
- 30・組立検査
- 31・製品検査技術者
- 32・補修
- 33・溶接
- 34・作業者
- 35・補修
- 36・外観検査
- 37・検査技術者による合否判定
- 38・補修
- 39・超音波検査
- 40・超音波探傷検査技術者
- 41・補修
- 42・仕上げ・矯正
- 43・製品検査
- 44・製品検査技術者
- 45・補修
- 46・塗装
- 47・出荷許可
- 48・発送
制作工程図
制作工程図とは、会社・工場の動きを一覧表にしたものを指します。
この表に符号を入れて番号では何をしているかを書き出していきます。
責任者の選出
人員配置の決め方になります。
必要資格を持った人員構成が構築できなければグレードは取得できません。
では、どのような資格が必要なのかどのような責任者の配置になるのかを自社のモデルケースで追ってみたいと思います。
部門 | 責任者・技術者 | 必要資格 |
品質管理部門 | 品質管理責任者 | 必要資格なし |
設計部門 | 工作図管理技術者 | 製作管理技術者1級または2級 |
外注部門 | 外注管理責任者 材料管理責任者 | 必要資格なし 必要資格なし |
製作部門 | 製作管理技術者 溶接管理技術者 溶接技能者 | 製作管理技術者1級 WES 2級 SA-3F・3H |
検査部門 | 製品検査管理技術者 超音波検査技術者 | 建築鉄骨製品検査技術者 建築鉄骨超音波検査技術者又は非破壊検査技術者NDI –UTレベル2 |
部門・責任者・技術者は会社によって名称の違いがあるかと思いますが、大枠似たような形になります。
資格をたくさん持っている人はどのポジションでもつくことができます。しかし、複数のポジションにつくことはできません。
中には兼任できる部分もありますのでよく調べて配置を決めましょう。
最低限必要な人数は決まってきますので、必要な資格を持った人員を配置できるように社内整備をしなければなりません。
1・設計図書(仕様書・設計図)
客先より設計図書を受け取り後見積もり作成をする。
見積もりは3次元CADを使用します。
受け取った設計図書に合わせて部材登録を行い、先行データを入力していきます。
入力が終わると登録された内容に合わせて必要部材、重量が算出されるようになります。
現場に関しても下見を行い、建て方時の搬入計画、経路、搬入車両の大きさ、道路の規制関係、道路使用許可は必要かなどみておく必要があります。
建て方時のレッカー配置検討、搬入車両の荷取り位置、現場の電線状況も判断して建て方可能かどうかを検討する必要があります。
工場加工においても製作可能な形、積み込み時の搬送荷姿も検討する必要があります。
2・製作会議(質疑事項/問題抽出)
受け取った設計図書に対して、自社で製作するにあたりどのような問題が出てくるのかを検討します。
製作工場(敷地面積、工場内設備)の能力・現場(製作工場にいる構成人員)の製作能力。これらを正しく理解する必要があります。
この二つの能力を正しく把握している前提で、可能範囲・不可能範囲(製作をできるか出来ないか。製作できない部分はないかどうか)を検討します。
不可能と判断されたものに関しては、どのようにすればクリア出来るのかを検討していきます。
設計事務所(元請け)に対して質疑応答を行い、問題点(不可能部分)は速やかに解消しましょう。
質疑応答は意外と時間がかかります。(客先解答がなかなか出てこない・設計者までの道のりが遠いなど)出来ることは出来る時に済ませましょう。
3・溶接計画
- 最大板厚の確認
- パス間温度の検討
- 積層図の確認
- 溶接姿勢の確認(MグレードはFまたはHまでの溶接方法になります。F=下向き・H=横向き溶接になる)
- FまたはHの姿勢で溶接できない箇所は出ないかの検討
大まかに上記を検討していきます。
これ以外にも物件ごとに検討が必要な部分は出てきます。
多くを見通すことができる経験・細かなところまで気がつける気配り・最後までイメージが出来るようになるまでは色濃い時間を過ごしたかどうかになります。
初めはわからないところから始まります。
たくさんの経験値を手に入れていきましょう。
検討後は製作要領書にまとめましょう。
4・検査要領
超音波検査試験を行うに関して検査不可部分はないかどうかを検討します。
例えば、3枚DFのサイコロの検査で平板部の捜査距離が足りない。
完成してからでは検査不可になる内DF・手がとどかなくなってしまう部分などがないかを検討する。
検査内容は設計図書を確認しましょう。
UT自主検査100%・第3者検査30%が一般的になりますが、設計図書に記載の通りになります。
第3者検査項目で外観検査の有無、隅肉溶接の検査の有無。
抜取り検査の場合は抜き取り率を確認します。
5・製作要領書
各部門で検討した結果等を合わせて1つにまとめていきます。
物件に合わせて制作要領書を仕上げていきます。
作成した要領書を客先へと提出します。
3部提出しますが、1部返却用として表紙に承諾印を押印済みのものを保管します。
これが今回物件の製作における取り決めになります。
6・工作図・加工図
要領書の承諾申請が済みましたら、要領書と設計図書に適合する加工図・工作図(施工図)を作成します。
設計図書の内容を再確認していき、施工内容を把握していきます。
7・照合チェック
施工図を書き終えたら、社内チェックを行います。
基本的には工作図管理責任者のチェックを受けることになります。
8・修正
是正箇所を直して再度「7・照合チェック」に戻る。
是正箇所がなくなるまで詰めていきます。
色々な角度から見てみると見えてくるものがあります。
多くの人に見てもらうことも必要になってきます。
9・承諾申請
社内で是正を行なった施工図を客先に提出します。
承諾申請を出し承諾を得る。
ここでは客先からの是正を受けることになります。
通称チェックバックという項目になります。
提出した施工図を赤ペンで消し込み(チェック)をして返してくる(バック)ことからきているものだと思います。
10・出図
承諾を得た施工図を各部門と共有する。
最近では「DX化」が進んでいる会社も少なくありません。
タブレットで共有して紙を無くす様にしているところもあります。
ただ紙の方が便利な場合もありますので、一概にこれが良いとは言えません。
便利な要素も多分に含まれています。
何をするにもチャレンジをしてみてください。
良いも悪いもとにかくやってみてから結論を出す様にしましょう。
11・鋼材・購入品発注明細
鋼材発注書を作成します。
発注書は相手(鋼材取引先)に何が欲しいかを伝えるための用紙(データ)になります。
各社のフォームがあると思います。
分かりやすく、見やすいものを渡しましょう。
思い違い・思い込み・勘違い・などのヒューマンエラーをできる限り減らしていくことが大事になります。
12・鋼材発注
- サイコロ加工指示書を作成
サイコロ加工指示書は施工図(設計図書)を確認後、使用するDF(ダイアフラム)の必要な板厚が満足しているかをチェックしていきます。
内容としては適応フランジの2サイズアップになるので、使用するH鋼のフランジ厚に対しての話になります。
サイズ違い等で生じる段差、主に下端の食い違いを満足しているかが確認項目の1つとして挙げられます。
コラムサイズの確認も必要になります。
符号管理をされていますので部材リストを確認します。
そして、1つ1つを確認しながら指示書を作成していきます。
指示書の作成が終わりましたら、必要なサイズ・個数・長さ(寸法)・材質を拾い出します。
加工指示書にまとめていきます。他者チェックを受けて発注になります。
絞りサイコロ
階を上るにつれてコラムサイズがダウンするパターンもあります。
どの様な方法でサイズダウンさせるのかをしっかりと確認しましょう。
- 板作りでサイコロを製作する。
- ダイアフラムを特殊な製品を使用する。
- メーカーで製作してもらう。
以上の3パターンが一般的な対応策になります。1つずつ見ていきます。
板作りでサイコロを製作する。
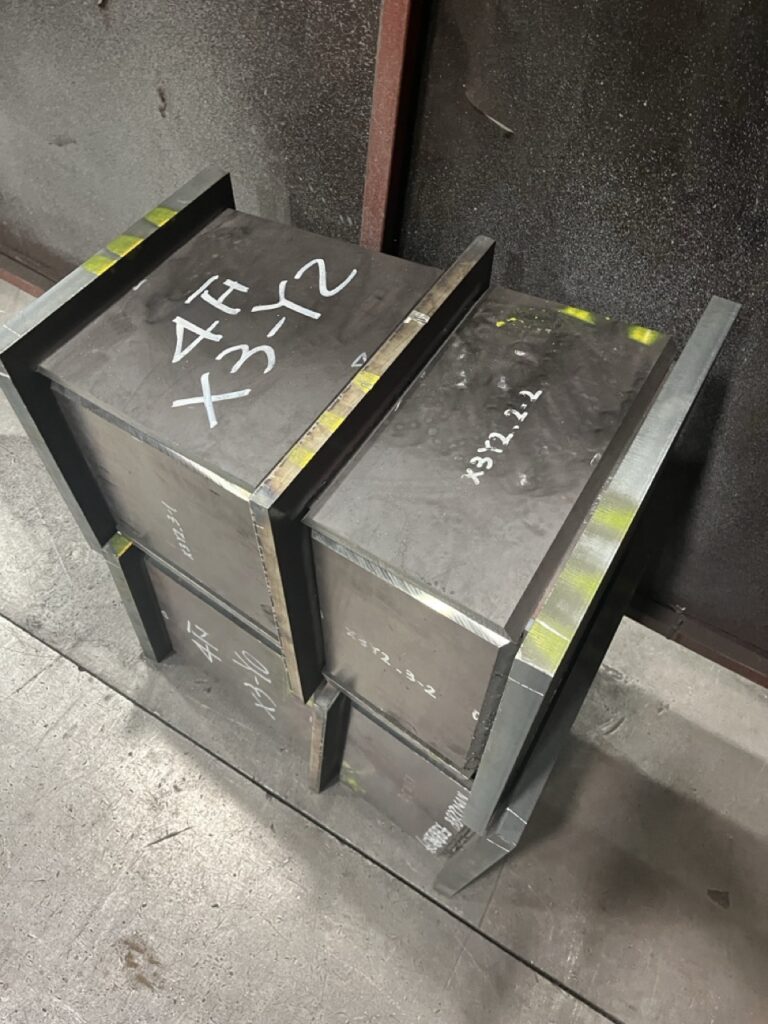
現寸作業を行いPL(鉄板)を使用してサイコロを製作します。現寸作業の際には次工程で組み立てしやすい取り合いに気をつけるなど注意点が発生してきます。
向き・方向など様々な点に気を配りながら材料を拾っていきます。
コラムの代わりになるPLは4枚とDFを両端に取り付けますので+2枚の計6枚。
PLとPLを繋げる方法は溶接です。
溶接方法はフルペネになります。(正式名称=フルペネトレーション)
フルペネには裏当てが必要になりますので各溶接部位に対して1枚用意します。
コラムで4枚、DFで8枚、シンプルな形状で最低でも12ヶ所の溶接が必要になります。
1の欠点としては手間暇がとにかくかかることです。
手間がかかるということは間違えるチャンスが多くなるということでもあります。
なるべくならば回避できる様にしたいところではあります。
ダイアフラムを特殊な製品を使用する。
既製品で「スマートダイア」(センクシア株式会社)を使用する。
このスマートダイアは設計事務所が把握できていて、設計図書にすでに反映されている場合は仕様に関して問題ありません。
設計図に入っていない場合は質疑応答を行なって提案していきます。
必要な応答を行なって設計者が許可を出した場合は使用が可能になります。
使用するサイズ・ダウンサイズ(絞り量)を確認して設計に合った企画をメーカーに検討を出します。
検討書、見積書の順で流れていきますので、発注をかけると入荷の流れになります。
使用するメリットはダイアフラムをこの既製品を使用するだけで絞りコラムと同じ結果を得ることが出来る点になります。
施工は簡単で一般のDFと同じ工程になります。
1つ問題があるとすれば、DFのサイズと上階のシャフトは同サイズではないので、どこにでも取り付けることが可能になることです。
勘違い、間違いは無いように気をつけましょう。
メーカーで製作してもらう。
コラムメーカーにお願いして「絞りコラム」を製作してもらいます。
四角錐の形でコラムを製作してもらい、あとはサイコロの製作と同じ工程を行うだけになります。
メーカーで製作してもらうメリットはコラムを製作してもらうのでコラム部分は溶接は必要がないので当然検査もありません。
DFは通常の切り板を使用できますので特殊な材料ではありません。
デメリットは少量では納期に余裕がないと頼みにくい点が挙げられます。
実際私は頼んだことはありません。納期が読める方に手を出してしまいます。
以上が絞りサイコロの種類になります。
色々なパターンの中から今回物件の最適解を見つけていきましょう。
DF(ダイアフラム)
必要枚数を集計します。
板材の寸法(縦x横x板厚)・材質(通しDFは基本SN490C)(内DFは490BかCで設計図書をよく確認しましょう。)拾いの結果を発注書にまとめていきます。
その中でも材質は大事な項目になるので重点的に確認をしておきましょう。
鉄は鉄なので、見た目で判断することはできません。
出荷証明(ミルシート)で確認する方法以外は色識別になります。
小口(切り口)にラインを引いて色と線の本数で材質は何になるのかをルールで決められています。
ラインが引いていないものは誤使用しないように最低ランクの材質にするようにも決められています。
裏当て(ワンピース)SN490B
FB -9×25を四角に曲げてある既製品をワンピースと呼び、コラムの切り口にセットするものを指します。
施工図を確認して、使用するサイズごとに拾い出しをしていきます。
コラムサイズは縦x横x PLの厚みごとで分けてカウントします。
1例として、ワンフロアのスタンダードはサイコロx1+シャフトx1で構成されます。この構成されているコラムは2本です。切り口は全部で4ヶ所になるので裏あては4つ必要になります。
なのでコラム1本で2枚の裏当てが必要になります。
この要領でサイズごとにいくつ必要になるのかを拾っていきましょう。
拾い出しが終われば発注書にまとめて発注になります。
コラム(BCR295)
サイコロ・シャフトを拾います。
階高より切り寸法を計算して算出します。
階高−サイコロの出来上がり寸法−溶接する隙間(裏当ての突き出し寸法)=シャフト長さ
取付したいH鋼の梁成(H鋼サイズ)+目違いの余裕(上下に3㎜ずつ)+縮み代(溶接1ヶ所につき1㎜)=サイコロの組み立て寸法
サイコロの組み立て寸法はH鋼サイズ+8㎜で求まります。
そしてサイコロ溶接を済ますと1ヶ所で1㎜縮む計算で処理します。ですからH鋼サイズ+6㎜になる計算です。
実際は縮んでいたり、いなかったり様々ですが、ルールとしてこの計算を成立させて寸法を算出します。
これを必要箇所数全てで行いサイズと寸法と必要本数を拾い出していきます。
最後は発注書にまとめて発注になります。
そのほか柱ジョイントがある場合は指示書に「これとこれが繋がります。」と分かりやすくしておきます。こうすることによって同部材からの切断で切り出してもらえるように指示をします。
目的としては、同一部材からの切り出しの方が形が同じになる確率は上がります。「目違い」という欠陥にならないように、なりにくくするためにできることはやっておきましょう。
欠陥になってしまうと直すのは大変です。最悪作り直しになってしまします。
ならないように細かなチェックが必要になります。
H鋼
施工図よりH鋼サイズを確認します。
長さ・数量・孔径・孔ピッチを確認します。
仕口であれば開先加工の有無を、そして開先向き(内開先を採用するのか)を確認します。
次にスカラップ加工の種類を確認します。
改良型スカラップなのかノンスカラップなのかを確認します。施工図や設計図書を見て確認します。
最後に同じものを別の人にも拾ってもらい、他者チェックを行いましょう。
書類の段階で間違いが見つかれば手直しは簡単に行うことができます。早期発見を目指しましょう。
間違いなく拾い出すことができていれば問題はありません。どのような方法でも構いませんので確認することが大事になってきます。
GPL(ガセットプレート)
製作図より必要サイズを拾い出します。
孔径・孔ピッチ・板厚・材質・合番(部品につける名前)を確認します。
現寸作業はCADで行います。床書現寸の時代ではなくなってきています。
汎用CADを使用しての現寸作業が当然になって来ています。
床書の知識・要領は絶対的に必要なスキルになるのですが、床書き現寸だけでは1次加工業者への発注はできなくなって来ています。
床書きを行うとセットで型取りを行います。
書いた現寸にフィルムを当てなぞって写していきます。
写したフィルムを切り板屋さんに持って行くか、取りに来てもらうかして形どった板を製作して貰います。
トレーサーという機械を使用したこの製法は現在CADに置き換わってきています。
CADはパソコンで現寸を書いてメールで送信します。
受け取ったデータで切り板を製作する流れになります。
フィルムを届けに行ったり取りに来てもらったりがなくなり時短になります。
少しずつ時間の使い方や作業環境が変わってきています。それにより近年製作スピードが飛躍的に上がりました。
GPLだけではなく色々な面でパソコンは必須になってきています。
ボルト
H.T.B(ハイテンションボルト)の種類は多くはないのですが、代表的なものをあげます。
- S10T
- F10T
- F8T
以上の3点は鉄骨屋では基本となるボルトの種類になります。
S10Tはシャーボルトと呼ばれ、ピンテイルと呼ばれる特殊な先端を有するボルトになります。
この先端は専用の締め付け機で締めると「締めました」の証として破断します。
破断することによってきちんと専用機を使用して締め付けたということがわかるようになっています。
F10Tは六角ハイテンションボルトと呼ばれ、ボルトの頭も六角になっています。
シャーボルトの頭はと言いますと、丸くなっていてスパナで掴むことはできません。
しかし、六角の頭はナットと同じ形をしています。性能としましてはS10Tと変わりません。
しかし、締め方が異なります。
締める力はトルクで表します。
本締め方法
1トルクコントロール法
2ナット回転法
上記、2点が本締の方法となります。
トルクコントロール法は専用機を使って締め付ける力をコントロールすることで破断する工程で確認することになります。
ナット回転法はナットを一定のトルクで締めて、その後さらにナットを回転させて本締めを完了させる方法になります。
回転角度が決められていて、120度±30度の範囲にとどめる事により所定の締め付けを得ることができます。
F8Tは六角ハイテンの溶融亜鉛メッキになります。
使用方法はF10Tと同様になります。ただしメッキをかけるために1度熱を加えるため強度が下がります。
そのため10ではなく8になります。この数字は強度区分になります。
ボルトの確認項目としては、継ぎ手基準図を確認します。
サイズ・長さ・必要本数を拾い出します。
階段・金物等本体ではない部分の拾い忘れに注意します。
スプライス
継ぎ手基準図を確認しましょう。
ジョイントヶ所数を拾い出します。
サイズごとに板厚・孔径・孔ピッチ・端アキ・ヘリアキを確認します。
フィラープレート等に特に気をつけることが必要になります。
フィラーは1㎜を超える隙間に適応になりますので、板厚の差が1.0㎜ならば必要はありません。
1.1㎜になった場合は必要になります。
この場合1.2㎜のPLを入れて差を埋め合わせる必要があります。
ブレス
平面ブレス・軸ブレス(ターンバックルブレス・アングルブレス等)を製作図を基に現寸を作図します。
現寸図より寸法を拾い出します。
電卓を使用して求めることもできます。
必要な計算方法は下記を参照して頂けますと幸いです。
90度のいわゆる直角三角形に適応になります。
寸法1x(電卓M+)寸法2x(電卓M+)(電卓MRC)(電卓√)=斜め寸法
寸法1を3000
寸法2を4000
として、√のついている電卓を使用すると求めることができます。
答えは5000となります。
母屋
施工図で母屋伏せ図を作図します。
使用部材・張り物・建物の最高高さを確認します。
母屋部材の必要長さを拾い出し、接続条件(ジョイント方法)を作図します。
取り合いピース(PL)を拾い出します。
使用ボルトの拾い出しをします。(表面処理・サイズ・長さ確認)
既製品のピースで間に合う場合は既製品を使用しましょう。
型鋼を使用して切断孔あけで使用する場合と、プレス加工で製作してもらう場合の2種類のピースがあります。
プレス加工で用意する方が安価である場合が多いので、設計図書等をよく確認をして要件・条件をクリア出来るように注意しましょう。
胴縁
施工図で胴縁図を作図します。
設計図書から使用部材を確認します。
客先より胴縁割り付けの指示を受け取ります。
これは張り物の継ぎ目になる(Wで受け材を入れる)位置を打ち合わせます。
継ぎ目の位置を明確に指示を受けていれば胴縁割り付けは大枠ずれる事はないでしょう。先に確認しておく事で後の施工図の是正が減ると思います。
その他にも、サッシ図・シャッター図面・庇図等を打合せて胴縁図を作図していきます。
客先へ胴縁図を提出します。ここでチェックバックを受けます。
是正をして承諾を受けます。
承諾を受けた図面で、使用するピースを拾い出します。
胴縁に使用する部材の長さ・本数・孔径・孔位置指示・表面処理(カラー・グレー・ダイマ・メッキになるならば黒)を確認して鋼材取り扱い加工業者に1次加工を頼みます。
使用するボルトは母屋と同様になります。
物件に合わせて使用するボルトを確認しましょう。
13溶接材料発注
溶接材料の種類の紹介になります。1例になります。
種類は他にもたくさんありますのでしっかりと調べて各社の溶接要領にあったものを用意しましょう。
規格 | 商品名 | 使用用途 | 棒径 |
YGW-18 | MG56(神戸製鋼) YM55(日鉄溶接工業) | 組立て+本溶接 | 1.2 1.4 |
YGW-11 | MG50(神戸製鋼) YM26(日鉄溶接工業) | 組立て+本溶接 | 1.2 1.4 |
YGW-12 | MG50T(神戸製鋼) | 組立て | 0.9 |
CW-111RB(ESAB) DS7100S(ESAB) | 鉄骨隅肉溶接 金物溶接 | 1.2 1.2 |
上記は弊社凡例になります。
その他にはアーク手溶接の溶接棒(通称手棒)がありますが、工場溶接では出番が少なくなっています。
半自動溶接の方が棒の継ぎ足しが無い分無駄が出難くなるのと、溶接効率が高くなります。効率が高いというのは溶接速度(溶接で使用する電流の流れ)が速くなります。
手溶接は現場で使用するのが主になってきます。
用意が比較的簡単にできるのと、被服が棒の外側に付いていてこの被覆は溶接と同時に溶解して溶着金属を酸化から守る薬になっています。
一方、半自動溶接は炭酸ガスを使用しないとブローホールという欠陥ができてしまいます。
炭酸ガスでシールドできていない酸化した金属は脆く品質の悪い状態になってしまいます。
14・購入品発注
購入品とは既製品を買ってそのまま加工の部品として使用する物を言います。
- 裏当て
- デッキ受け
- エンドタブ
- ネットフックなど
裏当て
FB-9×25(SN490B)で長さに切られた物になります。
使用目的は仕口の開先用で、ただ長さに切られた物をストレートと呼称しています。
また、ノンスカ用裏当てもあります。
仕口のスカラップ形状に合わせて拾い分けます。
ノンスカ用は仕口1本に対して4本必要になります。改良型は2本用意します。
必要な長さ・本数を発注しましょう。
デッキ受け
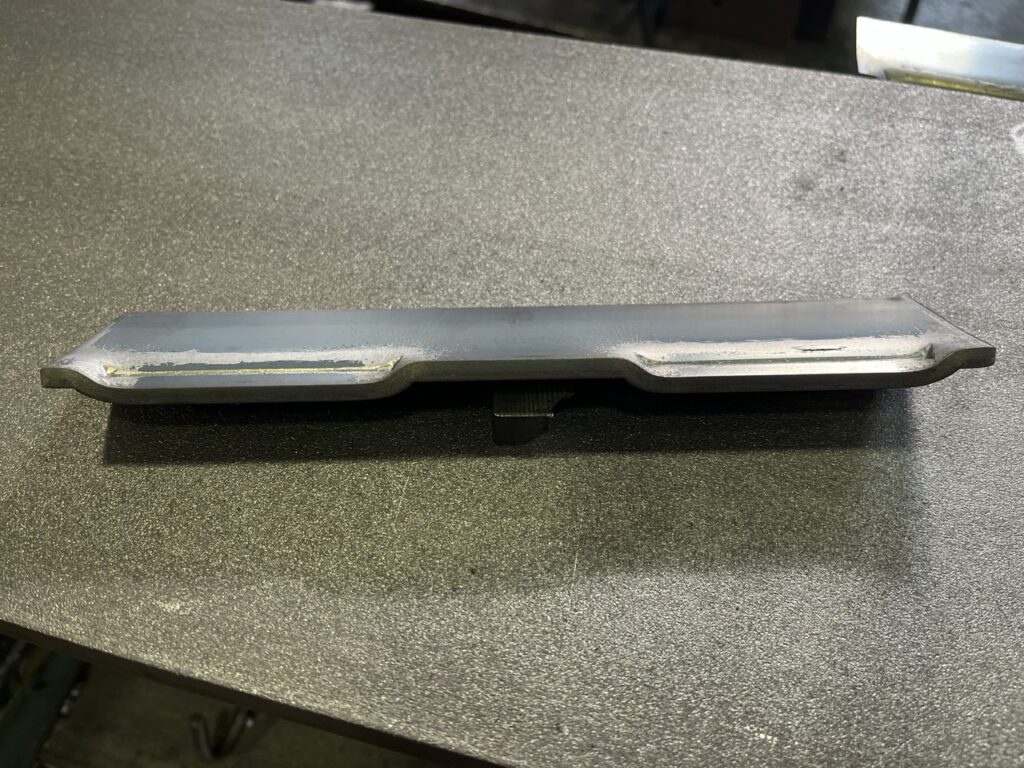
FB-6×50をプレス加工してある既製品になります。
スプライス部分のデッキは切り欠きを入れないと敷き込めないので切った部分の落っこち止めの役割をします。
スプライスの長さによって使用長さが変わってきます。
200〜350までの長さで、50刻みで寸法があります。
現状4種の中から必要な長さと枚数を用意します。
エンドタブ
仕口の溶接などのフルペネの両端部に使用します。
弊社では「コーナータブ」を使用しております。
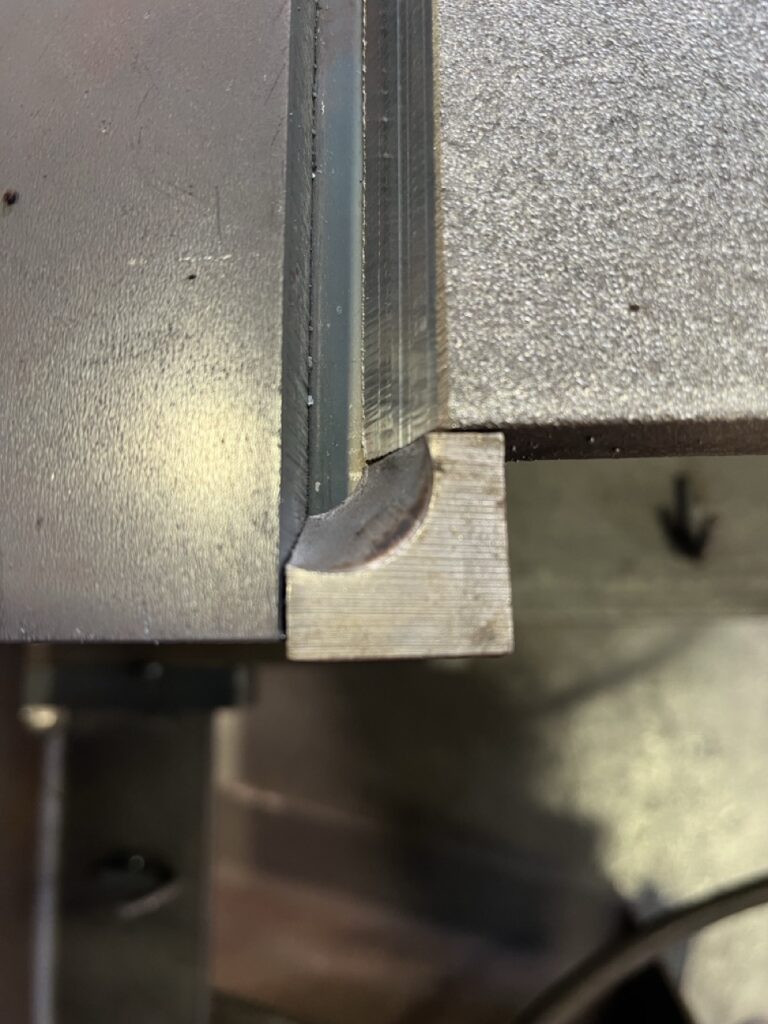
端部に鉄のこぼれ止めを付けます。
本来の使用目的はスタートとエンドの溶接欠陥をこのタブの中に逃して、健全部を確保しようというのがエンドタブの使用目的になります。
ネットフック
ネットフックの形は色々とお多いため使用する形状の確認をしましょう。
特に溶接長さが短くなってしまう形状もあるため、客先の指摘を受けてしまうものもあるかと思います。
物件に合わせて形状をしっかりと確認しましょう。
15・入庫・受入検査
各発注先より1次加工品や購入品が入荷されてきます。
材料管理責任者は入荷されてくる品物に対してチェックを行います。
員数・数量・寸法・サイズ・孔径・孔ピッチ・表面処理などの検査項目が挙げられます。
- 表面処理に関しては、1時加工品のH鋼であればショットブラストの表面荒さの確認。
- メッキ用加工品であれば、孔ばりの除去。
- C型等の軽量等であれば、カラーかグレー
などチェック項目は各会社・団体での決まり事があります。
下の写真はショットブラスト加工の状態になります。
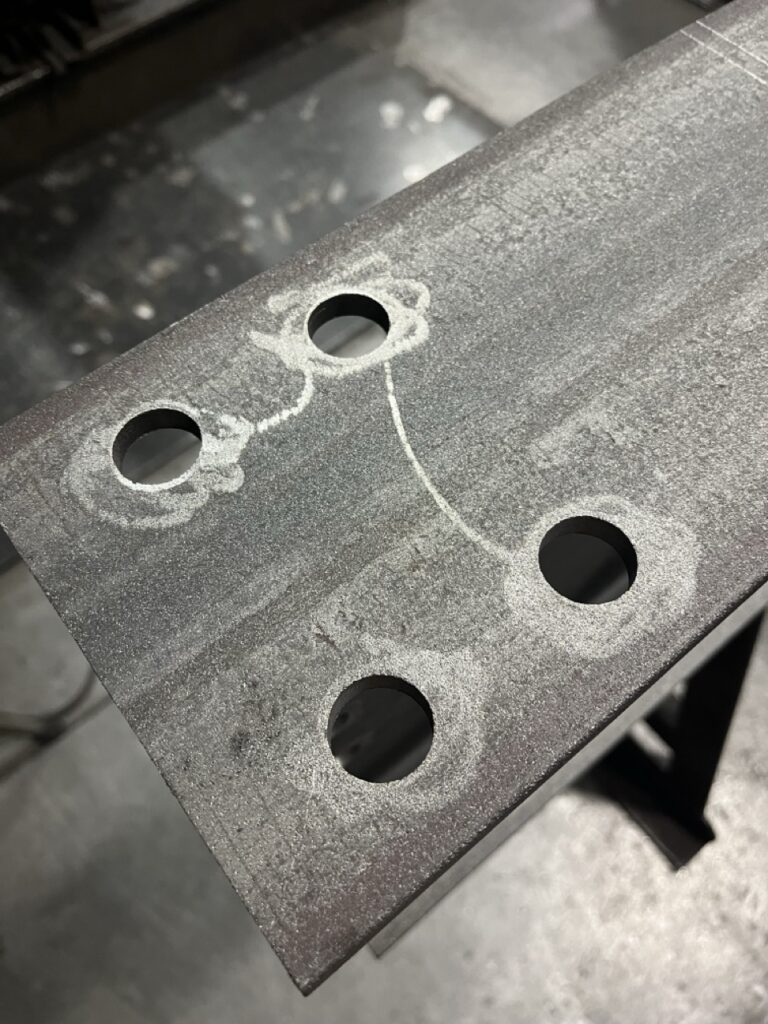
16・作業者(材料管理責任者)
1次加工品の受け入れは、材料管理責任者のチェックにより加工品の良否が判断される。
合格品は受け入れを行い、不合格品は再加工指示書を1次加工者にその旨伝える。
再加工品を受け入れる時は、15・入庫・受入検査に戻り再度チェックを受ける。
17・溶接材料・購入品の受け入れ
不良品が出た場合は仲卸業者に連絡を入れて、対応の指示をします。
受け入れは、品物確認・数量確認を行います。
18・裏当て加工
裏当て(ワンピース)を組み立てます。
1本の曲げ加工できていますので、繋ぎ目を溶接して資格に固定します。
4方の曲げた部分に「出っ張り」が生じてきますので、サンダーで除去します。
仕上げた面が平らになっている事が肝要になります。
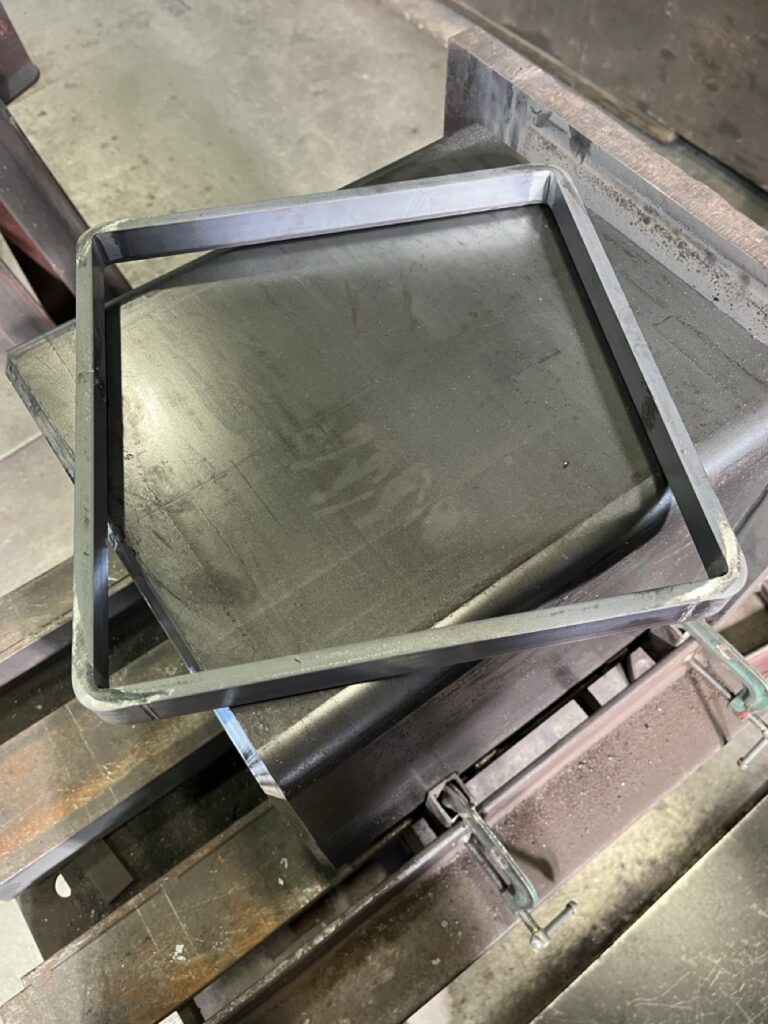
19・DF(ダイアフラム)加工
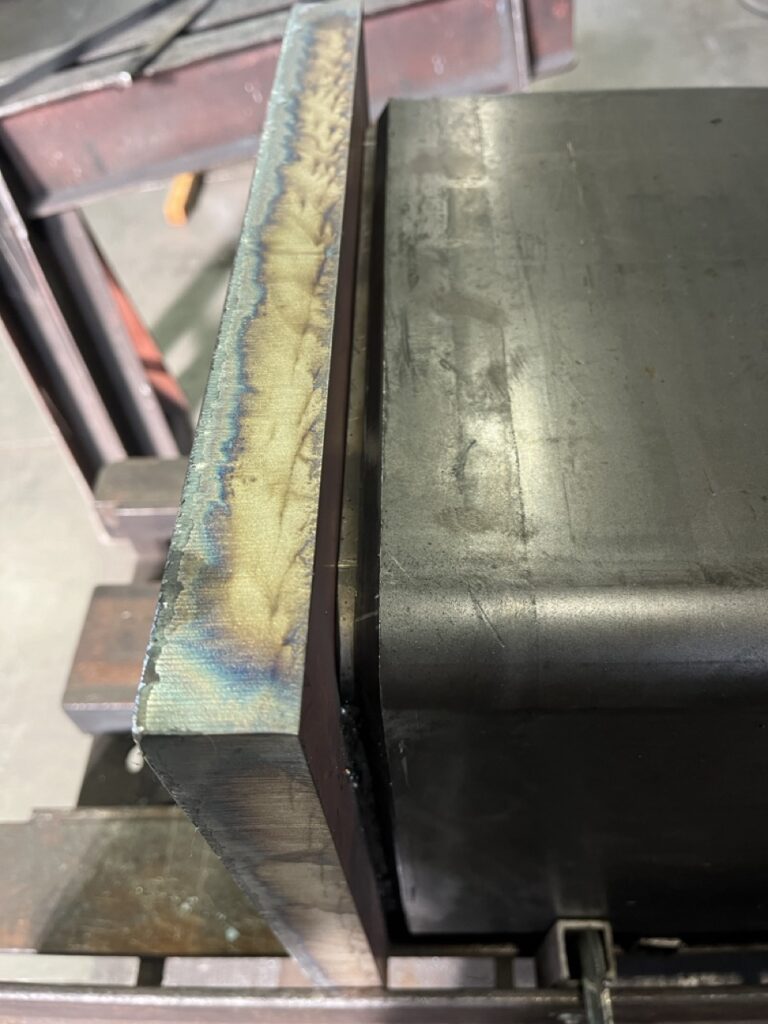
平面の真ん中あたりに5Φ程度のガス抜き孔を開けます。
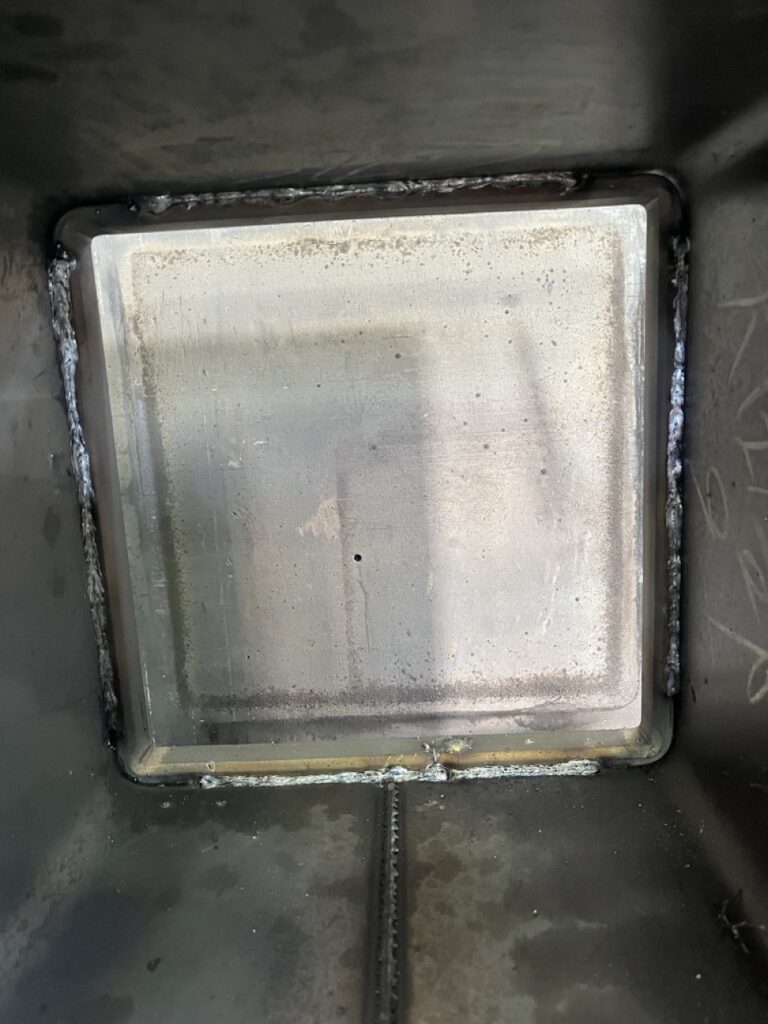
溶接の熱で空気は膨張します。密封してまうと膨張した空気は破裂しようとしますのでぬき孔が必要になります。
20・サイコロ(コラム)加工
サイコロの切り口両端部にある「シーム」をサンダーを使用して除去します。
裏あてが密着できるようにするためで、30ミリ程度仕上げます。
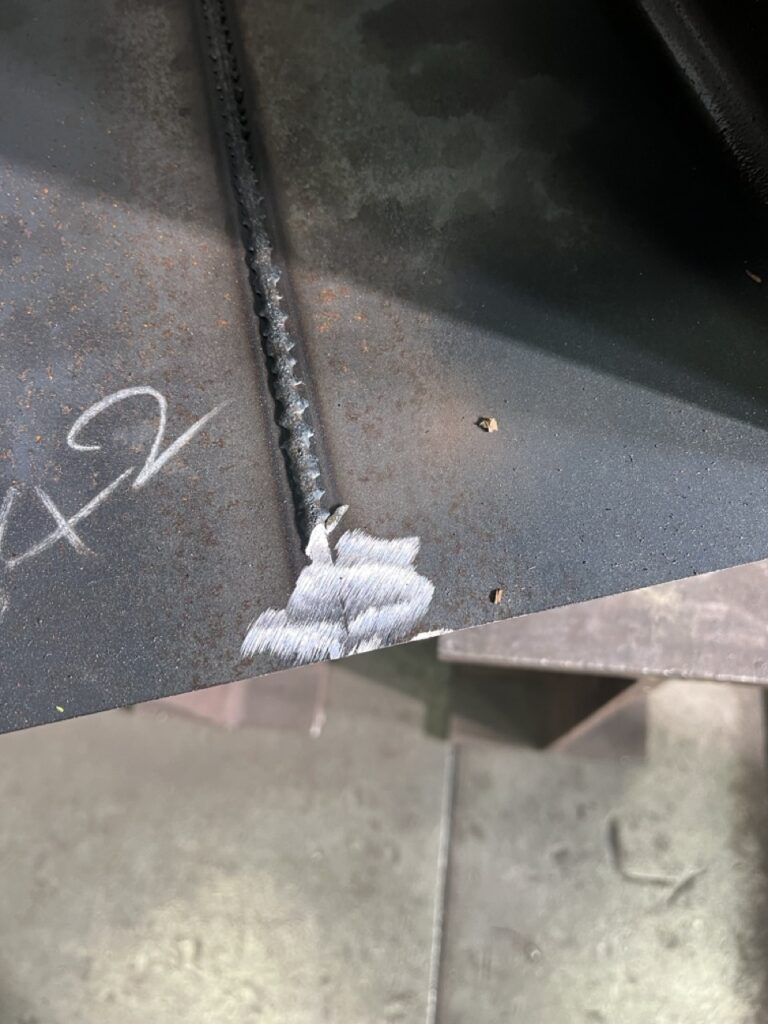
21・H鋼(仕口)加工
H鋼にGPL(ガセットプレート)を取り付けます。
罫書き→組立て→溶接を行います。
片持ち梁に使用されるCGなどが多いですね。
その他、剛接梁に使用する仕口の切り込みなどを指します。
仕口の組み立てに必要な前段取りをここで行います。
22・スカラップ加工
斜めの仕口などは開先加工を1時加工で出来ないため手動で開先加工を行います。
開先加工には2種類あります。
- 改良型スカラップ加工
- ノンスカラップ加工
改良型は裏当てが1本で貫通する形状になりますが、ノンスカラップは2本の裏当てを使用するようになります。
下図がノンスカラップの取り付け状況になります。
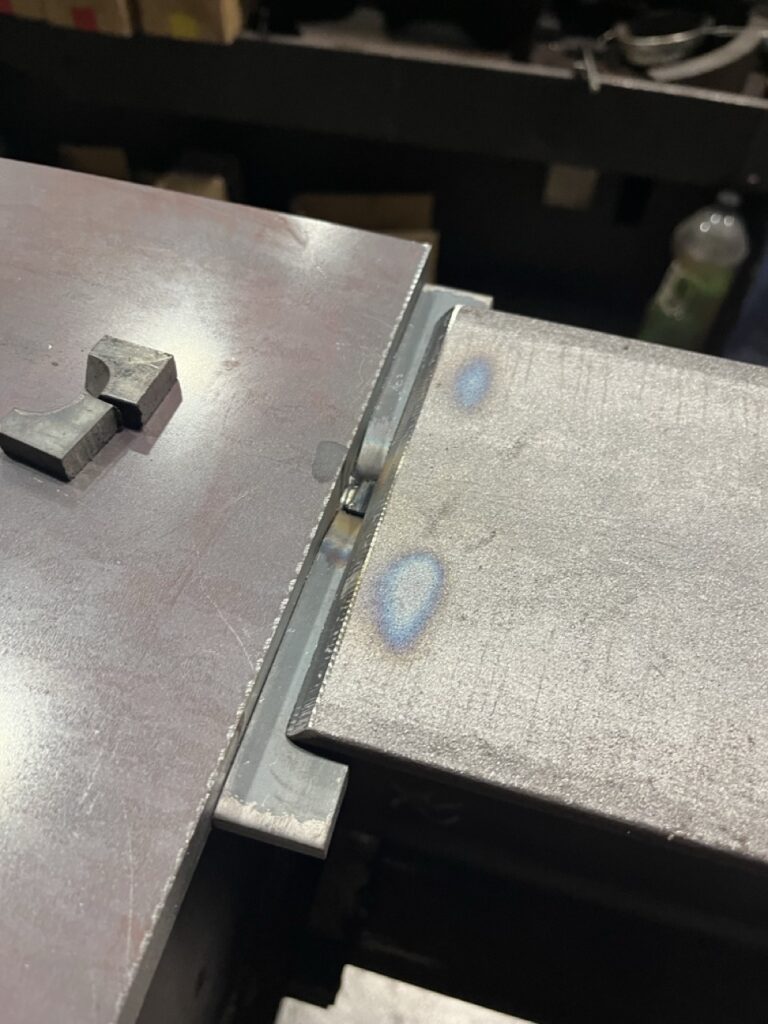
自社で開先加工を行う場合にはノンスカで加工することをおすすめします。
手数が少ないことで加工能率が上がるようになります。
裏当ての用意は数が増えますが、改良型を加工するときに必須のサンダーを使用して形状加工(サンダー掛け)は地味に時間がかかります。
サンダーの手間よりも裏当ての用意の手間の方が簡単に行えることから、ノンスカを推奨します。
ただし、注意点としてはH鋼のサイズの小さいものはスカラップ加工で1次加工を行うと溶接可能な部分がなくなってしまう場合も出てきます。
その他にも剛接梁の仕口の開先取で改良型を採用しようとした場合、うまく取り切らない状態がでてきます。
結果をイメージしてどの加工方法を採用するか検討する必要があります。
必ず裏当ての用意をすることを忘れないようにしましょう。
23・シャフト加工
両端部のシームを除去します。裏当てを取り付けできるようにします。
裏あてを取り付け後は、BPL(ベースプレート)を取り付けます。
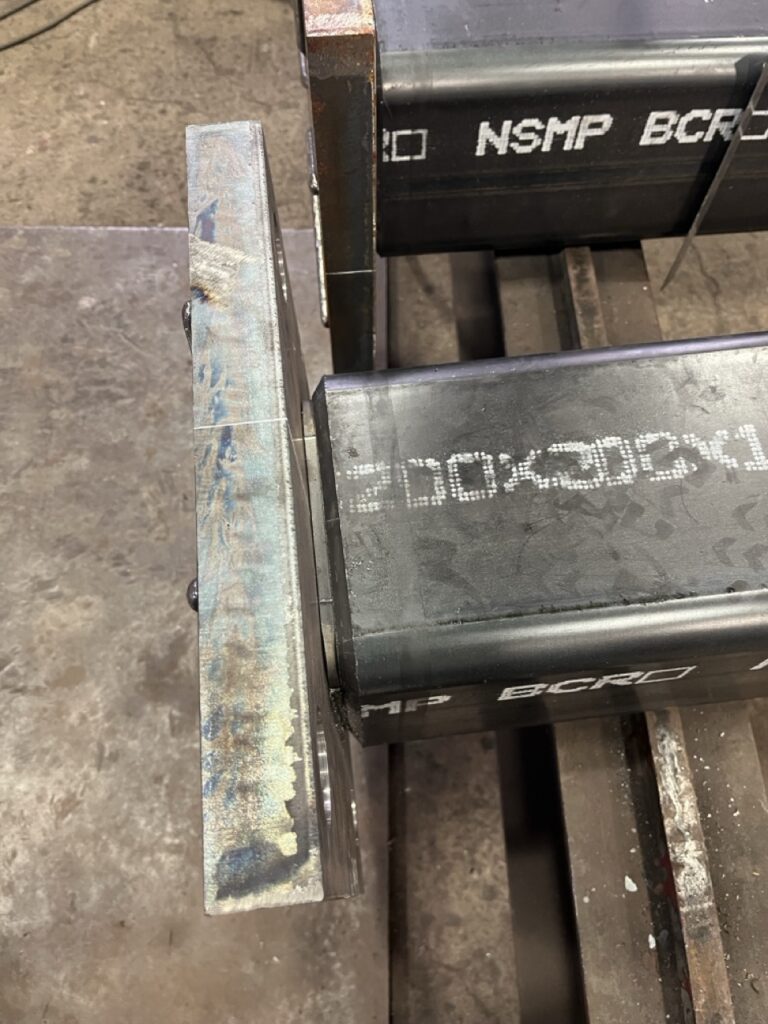
その他、柱ジョイントが発生する物件ではエレクションピース(柱のジョイント部分の名称)の取り付け。施工図の継ぎ手詳細図を確認します。
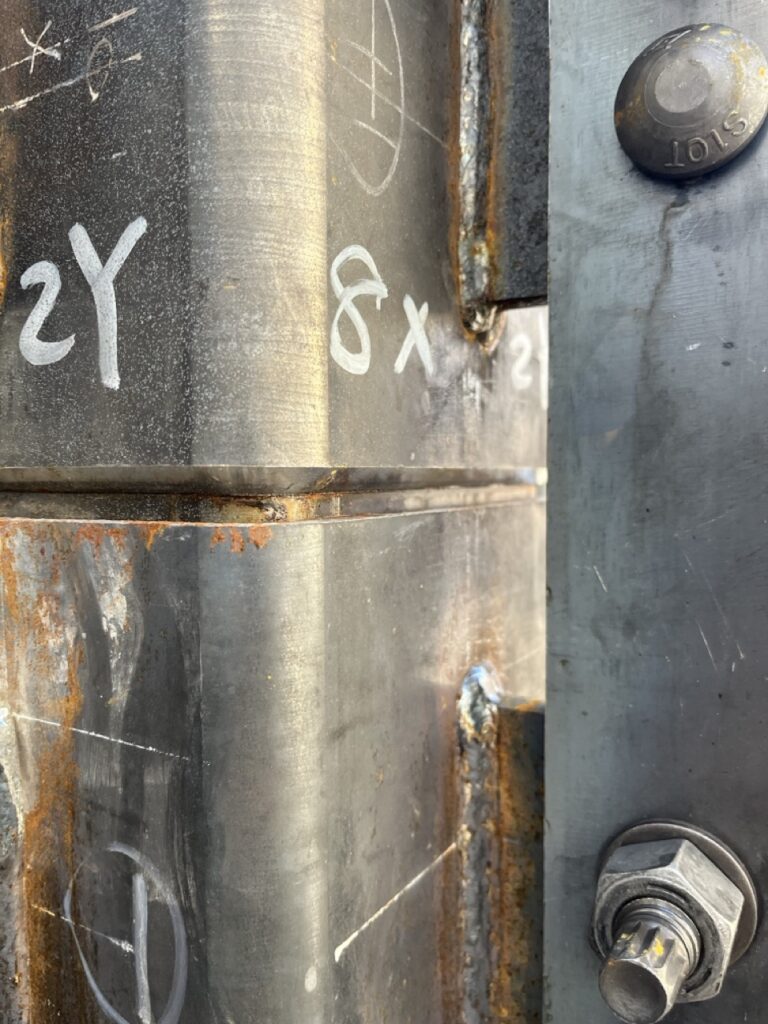
板厚の薄いコラムにエレクションピースを取り付ける場合、溶接の熱で曲がってしまう。このようなことが予想される部分に関しては曲がり止めの措置を講じて、変形防止に努めることを忘れない様に気をつけましょう。
変形が著しいと後の工程でジョイントできなかった。ジョイントは出来たけど、目違いの許容範囲を超えてしまい検査に合格できなかった。
などの弊害が予想されます。
直すのは時間と手間が非常にかかります。素直に加工できる時間を1とするならば、3倍以上を覚悟しなければいけません。そうなるだろうと想像してそうならない様にするには何が必要なのかをイメージする。これが出来るようになるにはたくさんの経験値が必要になります。
他人の仕事を見て、聞いて自分の判断材料の選択肢を増やしましょう。
その判断が合っているかは実践して取捨選択を繰り返していき、自分の成長へと繋げていきましょう。
24・加工
ここでの加工は組立て前の作業全般を指します。
内容としては、製作工程図の18〜23に記載しています。
物件に合わせて用意することになりますので、施工図をよく確認して準備不足の無いようにしましょう。
25・作業者
製作工程図の24加工を行うメンバーを指します。
26・補修
CG組立て等の間違い、溶接の外観不良の手直し行う。
手直しが終わった製品は次の工程へ進む。
27・組立て
- サイコロの組み立て
- 仕口の組み立て
- 梁の組み立て
- 柱の大組
大きく分けると4つの組み立てになります。
サイコロの組み立ては仕口を組み立てる前に行う工程になります。
サイコロの溶接まで完了していないと仕口の組み立てには移行できません。
なのでここのサイコロの組み立ての範囲はサイコロの溶接までになります。
仕口の組み立ても同様で溶接まで完了したものをさします。
弊社ではサイコロと仕口が組み上がった状態を「コア」と呼称される場合が多いです。
工程が進むにつれて部品数も多くなり形が変わってきます。
変化した形工程によって呼称も変わってきます。
この状態はこの呼称でというルールはないのですが、そのような呼称もあると捉えておいてください。
各社独自の呼称があると思います。ただ教科書(JAS6)に出ているのが正式な呼称になります。
柱の大組もコアの組み立てが終わってないと進んで行けません。
28・作業者
27の組み立ての内容を行う作業者を指します。
作業者同士の相互チェックが肝要になります。
お互いに指摘し合える環境と関係を大事にしましょう。
29・補修
- 組み立ての作業中に発生した間違い
- 作業者同士でのチェックで発見した間違い
- 製作図の間違い
- 追い出し寸法の入力間違いなど
そのほかの間違いもあると思います。
どのような方法のチェックが各社、各人に適合するか試してみましょう。
補修を終えた製品は28へ戻ります。
30・組立検査
28作業者で組み立てられた状態の製品を検査技術者が確認します。
確認項目は以下になります。
- サイコロ組み立て
- 仕口組み立て
- 梁組み立て
- 大組
これらを自社のチェックシートを使用して、各ブロックでの向き取り検査を行います。
抜取り検査はランダムに選定して検査を行います。
不合格が出なければそのまま先の工程へと進みます。
出た場合はさらに抜き取りを行い検査を重ねます。
不合格が続くと、最後には全数検査にまります。
31・製品検査技術者
製品検査技術者が30の内容を行います。
合格品は33へ
不合格品は32へ
32・補修
31で不合格になった製品は補修を行います。
手直しを行い完了した製品は再度31へ戻り検査を受けます。
33・溶接
31の検査を合格した製品は溶接技能者によって本溶接を行います。
各物件の溶接基準図を確認しておきます。
隅肉溶接の脚長、適応する溶接方法を確認をして溶接作業を行います。
34・作業者
ここでの作業者は33の作業内容を指します。
有資格者を配置できるようにしましょう。
35・補修
34の作業者が行った溶接業務の補修になります。
自己チェックと相互チェックを行った結果、不合格になった部位に対して是正を行います。
ここでの内容は外観検査になります。
- 脚長不足(余盛り不足)
- アンダーカット
- オーバーラップ
- ブローホール
- ピンホール
- ビード不整
などが挙げられます。
これらの補修には手棒溶接が多く用いられます。
手棒溶接は余盛りが少なく、溶着金属が整形しやすくなります。
手直しに使用する溶接方法も時と場合によって選定を行いましょう。
36・外観検査
検査技術者による外観検査になります。
35の内容を検査技術者が行います。
検査箇所数は全数検査で、抜け漏れの無いように検査を行います。
JAS6の鉄骨制度検査指針に沿って合否判定を行います。
37・検査技術者による合否判定
検査技術者によって判断された製品を意味します。
不合格ならば38へ、合格ならば39へ進みます。
38・補修
37で不合格になった製品は補修を行います。
手直しが終わった製品は37の検査技術者の合否判定に戻ります。
39・超音波検査
超音波探傷検査を行います。
溶接枚部欠陥を探傷していきます。
内部欠陥を発見した製品はNGとなり、41の補修に進みます。
40・超音波探傷検査技術者
検査技術者は探傷を行い、NGが出た製品は補修をします。
41・補修
内部欠陥を補修するにはアークエアーガウジングを使用します。
コンプレッサーとアーク溶接の合わせ技になりカーボンスティックを使用してスパークをさせます。
溶けた溶接部を圧縮したエアーを吹き付けて弾き飛ばしていきます。
ガウジングは音と埃が凄いので、保護具を着用しましょう。
中でも耳栓は装備するように気をつけましょう。
長い年月をかけてだんだんと耳が遠くなっている人をこの業界では多く見かけてきました。
自分を保護するのも仕事を続けていくのに必要なになります。
42・仕上げ・矯正
40を合格した製品は仕上げ(清掃)・矯正(歪み直し)を行います。
清掃は塗装前に埃や油分を落として塗料が付着しやすくなるようにします。
矯正は溶接の歪み取りで、バーナーを使用したり、真っ直ぐになるように押し引きをレバーブロックや天井クレーンを使用したりと試行錯誤します。
バーナーの加熱は温度管理が必要になりますので温度計や、温度チョークを使用します。
溶ける直前まで加熱して一気に水を掛けると温度差で歪みは入りやすくなりますが、組織形態が脆くなってしまうので、空冷と水冷の適用範囲が決められています。
直すには効果的になりますが製品には悪い結果を残してしましますので、製品が曲がらないように溶接の歪みと反対方向にテンションをかけてから溶接を行うのが一般的になります。
曲がらない工夫と溶接時順序を計画しましょう。
計画を立てるにも経験による見通しが必要になります。
43・製品検査
客先立ち会いの元、第三者により報告を行います。
検査内容は社内検査を100%(外観・超音波)行い、その製品を今度は第三者(第三者とは客先から派遣されて来る検査機関を言います)が30%を幹取り検査するのが多いパターンになります。
ただし、全てが30%かどうかは決まっていませんので、設計図書を確認しましょう。
書いていない場合は設計事務所、または元請けの担当者に質疑応答を行います。
社内検査は例外無く外観・超音波は100%になります。そのほかにも社内検査表の提出は必須になりますので検査表作成を行います。
検査内容は寸法検査・外観検査・超音波探傷検査になります。
社内検査表が出来上がれば、客先に提出します。
第三者の検査表は別で提出になります。となると
「第3者が提出するのだから社内検査表はいらないのでは?」と聞こえてきそうですが
社内検査表の内容は100%の検査率になります。その社内検査表の内容の裏付けとして別の検査者(第3者)が検査をランダム抜き取りで検査をします。結果異常は無かったので社内検査の結果は信用できます。という前提が含まれていますので社内検査表の提出は必要になってきます。
44・製品検査技術者
製品検査技術者は製品の合否を判定します。
製品検査で不良を認めた場合は補修を行います。45へ進む。
合格した製品は46へ進む。
45・補修
44で不合格と判断された物は合格になるように補修を行います。
補修が完了した製品は44で再チェックを行います。
あまりに大きなNGはこの段階では考えにくいので軽微な手直しを想定しています。
この段階での大きなNGは作り直しの可能性が大きいです。
部材の間違い、材質違い、そもそもの図面の間違いに誰も気が付かないまま、ここまできてしまった。
なんて事のないようにチェックを多岐に渡り行っています。
ミスはどの段階で気がつくのかで重症度が変わります。
早く気がつけば早いほど軽傷になります。
ミスをしないに越したことはありませんが、人間なのでどこかで必ずミスする物だと思ってチェックを行いましょう。
46・塗装
44の製品検査を合格した製品は塗装を行います。
塗装を行う前には必ず清掃を行います。
素地調整と言い種類があります。
1種と2種があり、それぞれ違いがあります。
1種は「ブラスト処理を行う。」
ブラスト処理を行うと錆が出やすい状態になります。
早期の塗装作業が必要になります。錆が出ればさらに錆落としを行う必要があります。
設備を持っていない会社さんもあると思います。協力業者へ依頼します。
機械の大きさに制限があると思いますので、機械に入る形状・寸法を把握した上どの段階で加工を指示するのかを判断します。
出来れば1次加工の段階でショットを出せれば問題は少なく済みます。
2種は「電動工具と手動工具を併用」
一般的にはこちらの2種が多いかと思います。
ブラスト処理ではなく清掃を行い塗装の準備をします。
次に、塗装範囲の確認を行います。
非塗装範囲の確立
テープ養生・カバーを使用して塗料の付着を防ぐようにします。
主な範囲としては、BPL下からのコンクリートに埋まる部分や、スプライスのジョイント箇所、現場での柱ジョイント部分など物件に合わせて確認をしましょう。
塗料の種類の確認
現在弊社で使用している塗料は大同塗料の2-Timese Coat(ツータイムスコート)
JIS K5674 1種 鉛・クロムフリー錆び止めペイント F★★★★
色は種類がありますが、赤錆色もしくはグレーを使用しています。
グレーと言っても薄い色から濃い色まで種類があります。その中でも一番濃い色の「N5グレー」を好んで使用しています。
選定理由としては汚れが目立ちにくいからです。ただし、他のグレーに比べてになりますが、
色の指定はあまりないので、基本的にはグレーを使用しています。
胴縁・母屋などの軽量物は赤錆(カラー)を使用する場合もあります。
基本鉄骨は「下地」になるので仕上がって来ると隠れて見えなくなってしまします。
カラー材とグレー材ではカラーの方が値段が安いので、ペンキで仕上げ鉄部が見えて来る部分は仕上げペンキの色を確認して明るい色ならば、赤錆よりもグレーを選定しましょう。
47・出荷許可
検査技術者が製品状態を確認して、代表に報告をします。
代表は報告を受けて内容と製品を確認した後「出荷許可証」へサイン、押印をします。
48・発送
出荷許可を受けた製品は積み込みを行います。
現場搬送を行い建て方になります。
最後までお付き合いいただきありがとうございます。
次回またお会いいたしましょう。